Flexible Printed Circuits
Flexible printed circuits were originally designed as a replacement for traditional wire harnesses. Today's trends including IoT, connectivity, mobility, wearables, miniaturization and more are driving rapid growth in the need for and use of flexible printed circuits across most every industry. A flexible circuit in its purest form is a vast array of conductors sandwiched between layers of very thin dielectric film.
From simple applications to the most complex, the versatility of flexible printed circuit boards are unmatched.
Flexible Circuit Technologies is happy to take on most any flexible circuit design challenge that you may have.
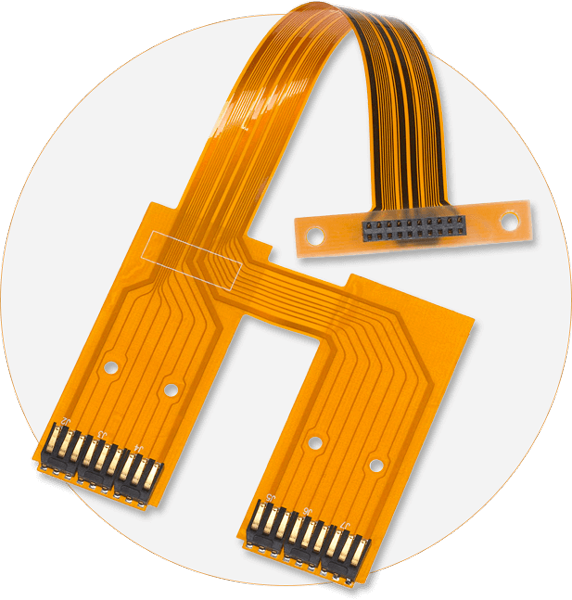
Flexible Circuit Technologies, a premier global supplier in design and production of
Flexible Circuits, Rigid Flex, Flexible Heaters, Flat Flex Cables, Membrane Switches, Plastic Moldings, Assemblies, Product Module Builds to Complete Product Box Builds
For more in depth information on Flex Printed Circuits, click on the links below:
As a connective device, the primary benefits of flexible circuits compared to traditional cabling and rigid boards include:
- Reduced wiring errors
- Elimination of mechanical connectors
- Unparalleled design flexibility
- Higher circuit density
- More robust operating temperature range
- Stronger signal quality
- Improved reliability and impedance control
- Size and weight reduction
There are many benefits to Flexible Printed Circuits including:
Assembly Error Reduction – With accurate designs and automated production, flex circuits eliminate human errors, when compared to hand-built wire harnesses. Circuits are ONLY routed to those points called for by the schematic, net list, or gerber files.
Decreased Assembly Time and Costs – Flex circuits require less manual labor during assembly and reduce production errors. Flex circuits have an intrinsic ability to integrate form, fit and function. Flex circuits eliminate the high cost of routing, wrapping and soldering wires. Wiring errors are eliminated and hence manufacturing costs are reduced. Whether it is a low volume production with a complex circuit or high-volume production with a simple circuit, assembly time and costs are decreased.
Design Freedom – Unlike rigid boards, flexible circuits are not restricted to two dimensions. Because they are as flexible as wires or ribbon cables, flexible circuit design options are endless. At Flexible Circuit Technologies, we pride ourselves on taking on the most complex of design challenges. Flexible circuits can be designed to meet highly complex and unimaginable configurations while being able to operate in the most hostile environments. Flex circuit designs could entail any of the following:
- Highly complex configurations
- Withstand hostile shock and vibration operating environments
- Complex interconnections
- Shielding
- Single layer, multilayer, and Rigid/flex capabilities
- Surface mounted devices
Wire harness conversion to flex reduces wiring errors from hand made connections and decreases assembly time
Flexibility during Installation – Flexible circuits allow a third dimension to work with because they can interconnect between two or more planes when formed. As a result, they solve space and weight problems unmatched by rigid boards. Flex circuits can be manipulated many times during installation and servicing without electronic failure.
High Density Applications – Flexible circuits allow for extremely narrow lines and spaces giving way to high density device population. Denser device populations and lighter conductors can be designed into a product, freeing space for additional product features.
Improved Airflow – Because of their streamlined design, flexible circuits allow for the flow of cooling air through an electronic application.
Increased Heat Dissipation – Due to the larger surface-to-volume ratio of the copper traces, and the ultra-thin electrical dielectric covering, heat generated in the traces is more readily dissipated. Further, the thinner design of flex circuits allows for heat dissipation from both sides of the circuit.
Increased System Reliability – In the past, most circuit failures occurred at an interconnection point. Flex circuits can be designed so that interconnections are reduced, which in turn, increases the reliability of a circuit.
Point-to-Point Wire Replacement – Depending on the number of point-to-point connections in a circuit design, at Flexible Circuit Technologies, we can design and build a single flex circuit that can eliminate many (if not all) of those interconnections.
Reliability and Durability – A properly designed dynamic flexible circuit can move and flex more than 1 million times without a failure.
Repeatable Routings – Our circuits are made from precise replicas of artwork for superior manufacturing consistency. The etched circuits replace the solder and hand wiring connections of the rigid board, completely eliminating wiring errors.
Simplified Circuit Geometry – Flexible Circuit Technologies places surface mount electronics directly onto the circuit which results in streamlining the overall production flow. Customers can get a flexible circuit fully assembled with all components.
Package Size and Weight Reduction – Thicker dielectric cores in rigid boards create more weight and consume more space. Flex circuits contain the thinnest dielectric substrates available. Thinness allows for a more streamlined design, eliminating the need for bulky rigid boards. The flexibility allows for overall package size reduction. In addition to package size reduction, package weight is also reduced. With the ever-increasing demands of the electronics industries, weight and volume reduction makes flex circuits an attractive interconnect solution.
Prior to designing a circuit, there are two fundamental structural applications that must be understood and/or that dictate material selection:
Static Application – An application where flexible circuits are flexed only to install the circuit and fit it into its application (also known as flex-to-install).
Dynamic Flexing Applications – A situation where the flexible circuit itself is dynamically (repeatedly) flexed during the actual use of the final product. Common examples include flip-type cell phones, laptops, printer heads and robotic arms. A dynamic application will require a very symmetrical material stack up and fully annealed copper conductors.
The benefits of flexible circuits are realized in most applications requiring high cycle flexing and/or a high degree of accuracy. Some common applications include:
- Air bag systems
- Automotive engine controls
- Antilock brakes
- Avionics
- Bar code equipment
- Battery packs
- Calculators
- Cameras
- Cell phones
- Heart monitors and pacemakers
- Fuel pumps
- Hearing aids
- Printers
- Motion systems
- GPS systems
- Satellites
Conductors – Copper is the most widely used conductor and comes in various thicknesses to meet each customer’s requirements. Conductor options include:
- Rolled annealed (RA) copper
- Electro deposited (ED) copper
- Carbon
- Silver ink
- Inconel®
- Cupro-nickel
- Constantan
Adhesives – Adhesive selection depends on customer needs and conductor thickness. Common adhesives include:
- Epoxy
- Acrylic
- Pressure Sensitive Adhesives (PSAs)
Insulators – Flexible substrate (base) and coverlay materials are available in a variety of thicknesses and from several manufacturers. Common insulators include:
- Polyimide
- Polyester, Polyethylene Naphthalate (PEN), and Polyethylene Terephthalate
(PET) - Solder mask
- Flexible solder mask
- Screen printed dielectric
Finishes – The final finish depends on each customer’s assembly requirements and the application of the finished product. Common finishes include:
- ENIG Electroless Nickel Immersion Gold (most common)
- ENEPIG Electroless Nickel Electroless Palladium Immersion Gold
- OSP Organic Solderability Preservative
- Tin
- Hard nickel/gold
- Wire bondable nickel/ soft gold
- Solder (Tin, Lead or RoHS compliant)
- Silver
As the flex circuit market continues to expand, there have been many advances in technology including:
Heat Sinks – Heat sinks can be laminated to flex circuits to dissipate heat away from sensitive components such as LEDs.
Component Assembly –We offer through hole and surface mount capabilities, as well as in circuit testing, conformal coating, and electrostatic protective packaging.
Controlled Impedance – With increasing signal switching speeds, engineers need to understand and control the impedance of signal paths. With short signal transition times and high clock rates of modern digital circuitry, traces need to be considered transmission lines instead of simple interconnections. Controlled impedance traces are designed to match impedance along the entire signal path to minimize electrical reflections and ensure an error free transition between the track and interconnections. Controlled impedance signal transmission requires tight control of not only trace width and thickness, but also dielectric thickness. At Flexible Circuit Technologies, we have extensive experience in designing and manufacturing flex circuits with controlled impedance.
Crimp Pins – Crimp Pins are mechanically attached a circuit to allow for soldered connections.
Graphic Overlays – Graphic Overlays can be placed over flexible circuits, rigid boards or membrane switches. The overlays provide the user interface with the underlying circuit and typically are used in conjunction with LEDs, LCD displays or dome switches mounted on the circuits. The overlays are made from polycarbonate, polyester or acrylic materials.
Laser Skived Slots and Holes – FCT uses precision lasers to create irregular shaped openings in the dielectrics, as well as excising the circuit outline. This allows Flexible Circuit Technologies to support prototype volumes without requiring expensive tooling.
Overmolding – Overmolding is the process by which FCT embeds the flex with assembled electronics into a variety of compliant polymers. As wearable or other electronic devices become more common, overmolded flexible assemblies can be a cost effective and rugged solution.
Pressure Sensitive Adhesives (PSAs) – PSAs with a release liner are used in applications where a portion(s) of the circuit needs to be secured to a specific location within the final product. During assembly, the release liner is peeled away and the exposed adhesive allows the assembler to press the circuit into place and keep it there.
Sculptured Flex Circuits – Sculptured flex circuits are special in that the copper conductors vary in thickness in different places. The copper is thin at the most flexible part of the circuit and thick at the interconnection point. Sculptured flex circuits allow for bare metal connections (like a plug in) and remain strong at the solder joint formation. Sculptured fingers provide a more reliable alternative to mechanically fastened crimp pins.
Stiffeners – Stiffeners are applied to flex circuits where additional support is needed such as areas of component assembly or underneath exposed traces that will be plugged in for connection. Common stiffeners are made from FR4 and polyimide.
Wire Assembly – In certain applications a combination of flex or rigid circuit with traditional wire may be a more economical design that still meets the needs of the customer’s subassembly. At Flexible Circuit Technologies, we have the capabilities to design, source, manufacture and assemble the entire subassembly incorporating the circuit, wiring and components.
Flexible Heaters – Flexible heaters are thin, bendable heating elements, shaped to fit your unique heating equipment needs. Flexible heaters can be designed to operate over a wide range of voltages and temperatures. Temp control devices such as thermistors, thermostats, or NTCs can be mounted directly to the flexible heater. Lead wires and connectors can also be added as required. Most flexible heaters are also supplied with a pressure sensitive adhesive backing for easy application.
Hot Bar Solder – Hot bar solder connection is a way to eliminate a connector set between the hardboard and the flex circuit. This connection provides an efficient, durable and less expensive alternative to a standard connector set.
In summary, if you have flexible circuit design or flexible printed circuit board needs, we can help.